
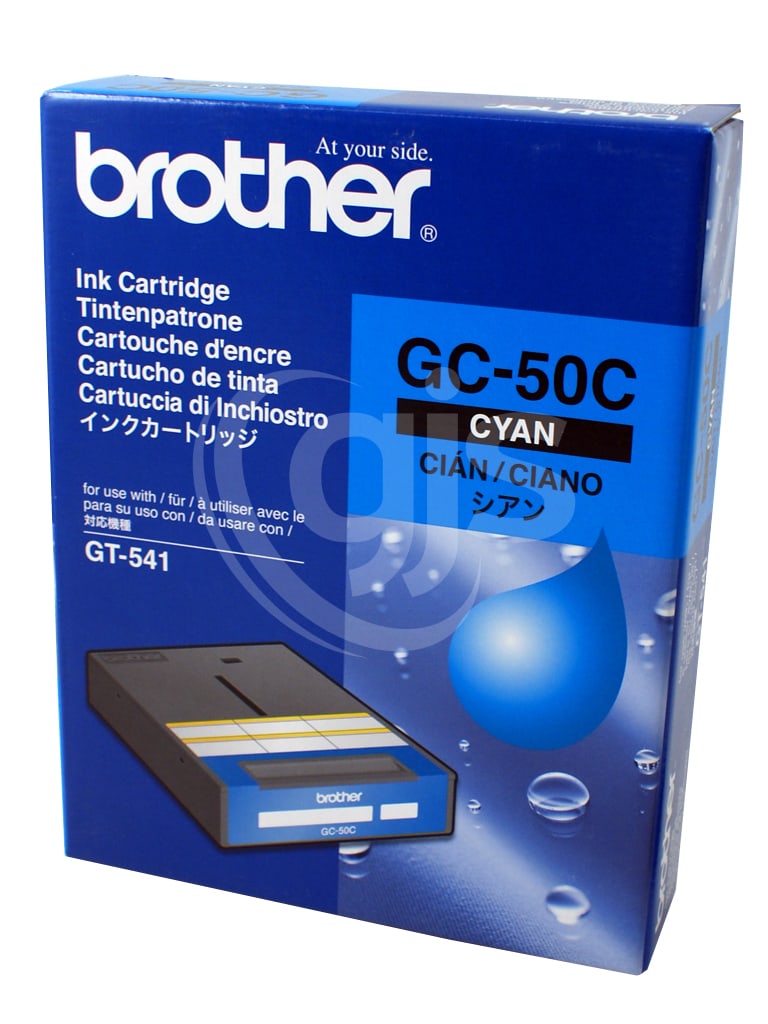
The shirt is then digitally printed according to the design in the printer queue.ĭirect-to-garment printing in the United States began in 1996 with the introduction of the first commercially available DTG printer named "Revolution", developed by DIS of Bradenton, Florida, and based on an invention of Matthew Rhome. Once the custom garment -for instance a t-shirt- has been properly pre-treated, the shirt (or garment) is then positioned onto a platten system designed to hold the shirt in place. This is especially important when using white ink on dark garments. The pre-treatment also allows the water-based inks to bond more fully to the garment. The pre-treatment is heat-pressed into the custom t-shirt causing the fibers of the shirt to lay down. In addition, pre-treatment is typically applied to the garment before printing.
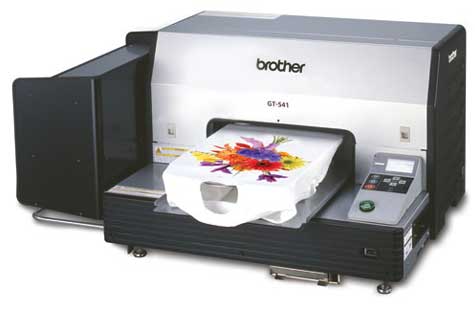
Since D2 inks are water-based, they work best for printing on natural fibers such as cotton, bamboo, hemp, and linen. Printing process ĭTG printers use aqueous textile inks (water-based chemistry) that require a unique curing process. However, unlike screen printing, there is no long setup or clean-up process, and DTG has the ability to print just one single shirt for minimal cost. Since this is a digital process the print is sharper and has a higher resolution, or DPI, than traditional printing methods such as screen printing.

Lays down loose fibers to provide for a smoother substrate.

Stronger bond between garment fibers and the pigmented inks.DTG printers typically have a platen designed to hold the garment in a fixed position, and the printer inks are jetted or sprayed onto the textile by the print head.ĭTG typically requires that the garment be pre-treated with a PTM or Pre-treatment machine allowing for the following: Direct-to-garment printing (DTG) is a process of printing on textiles using specialized aqueous ink jet technology.
